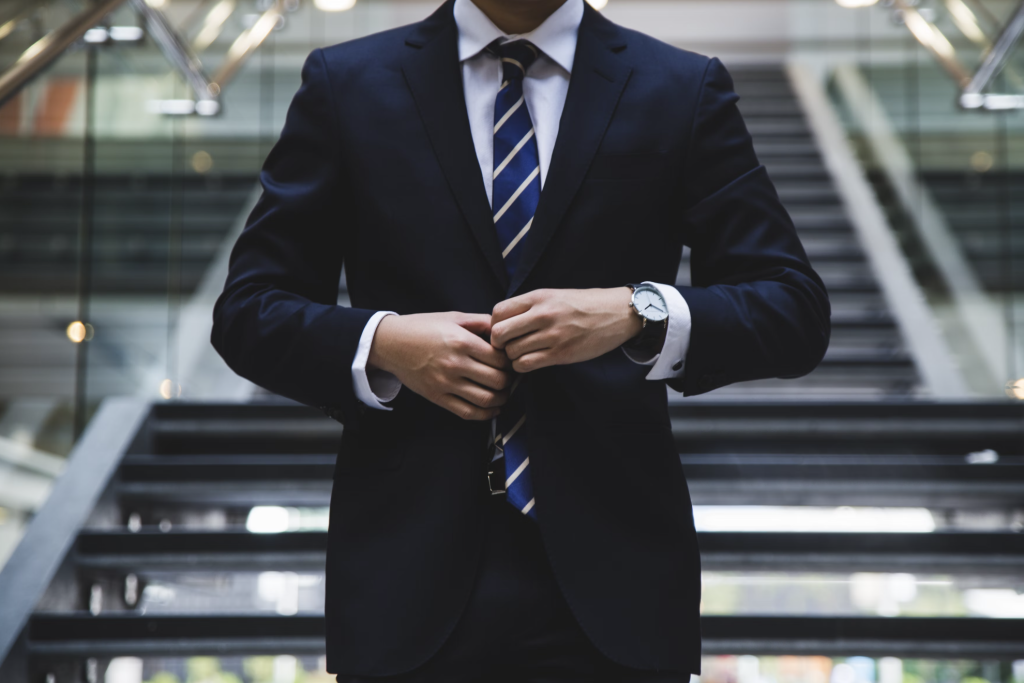
Can management really be the key for companies to compete and increase productivity?
While thousands of books and articles are written about “leadership”, there is something critically important that gets much less attention. This is the day-to-day practice of management. Leadership sounds aspirational, even heroic, whereas management has a much less appealing ring to it. However, leadership is not something that can exist in a vacuum; for an organization to achieve its goals, leadership must be founded on the ability to manage effectively.
Is management a science?
The word “management” is derived from two Latin words: manus, which means hand, and agere which means to act. In other words, management is a hands-on activity. In every organization there are people who are called managers, but often they have little education or training in management as a practice. They are simply “in charge”. A more “scientific” way of organizing work was introduced in manufacturing industries at the end of the nineteenth century. These were attempts to achieve higher levels of efficiency and productivity related to time and motion. This approach is often referred to as Taylorism after Frederick Taylor. Criticism of this approach was that it was dehumanizing, treating the worker as a cog in the wheel of production. In his 1903 work “Shop Management’, Taylor states:
“The art of management has been defined, “as knowing exactly what you want men to do, and then seeing that they do it in the best and cheapest way“.
Societies have evolved since 1903 and such an assertion would no longer be acceptable.
New science for management: a very brief history
Not only society but also science has evolved. The mechanistic understanding of nature that we find in Galileo, and later Newton, enabled mankind to make all the scientific and technological progress up to modern times. However, new discoveries were made towards the end of the nineteenth century that classical theory was unable to fully account for, such as the discovery of the electron and radioactive matter. It would take Einstein’s Theory of Relativity and Quantum Mechanics to indicate that by the 1920s, a “new physics” was necessary, one that was not deterministic but probabilistic. Subsequently, towards the middle of the twentieth century, a new understanding of nature began to emerge: one of complexity.
Warren Weaver was a mathematician and co-developer of the Shannon -Weaver model of communication. During WWII, he was Chief of the Applied Mathematics Panel at the U.S. Office of Scientific Research and Development where he directed the work of mathematicians in Operations Research. In a 1948 American Scientist article on “Science and Complexity” he argued that the mathematical methods which had led to great success in science were limited to “problems of simplicity”. Weaver recognized that there are complex problems of “disorganized complexity” that require investigation of a system where the parts are in close interrelation. This calls for the mathematics of statistical mechanics.
Science must, over the next 50 years, learn to deal with these problems of organized complexity [problems for which complexity “emerges” from the coordinated interaction between its parts]. (Weaver 1948.)
In all the sciences, there is progressively a new understanding that represents a paradigm shift from a mechanistic way of interpreting reality that looks at “pieces” to one based on understanding interactions. Complexity science, systems science and network theory are now established fields of research.
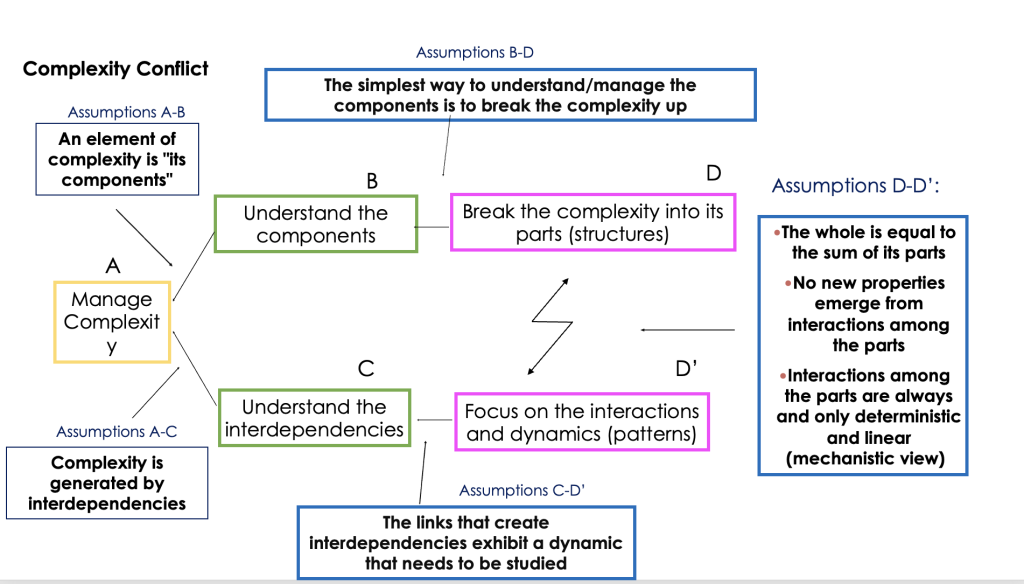
What has all this to do with management? Looking at the programs in Business Schools, there is little trace of these fundamental shifts in the investigation of nature that are shaping our world and how we understand it. This is a serious omission as it is increasingly clear how much we are all immersed in complexity, i.e. a web of interconnections. We are all embedded in networks of networks and yet most companies still design themselves as top down hierarchies and base their finance on cost accounting. This approach is no longer adequate. It is not a question of adopting a new fad; it is a matter of understanding and adopting an approach that is the most appropriate way to deploy available resources and improve performance. A lack of understanding of complexity with all its implications for management will inevitably lead to sub-optimization of resources and energies in any company. In a world of fierce competition for market share, sub-optimization is something that no company today can afford.
Unveiling the inherent nature of any organization
It would take the work of a physicist, statistician and engineer to apply a new, systemic understanding to management in a highly practical way. In the 1950s, Dr. W. Edwards Deming was sent to Japan to help industrialists recover from the devastation of WW II. There are two fundamental elements in what he taught the Japanese that propelled them to economic success. The first element is that an organization is a system: a network of interdependent components that work together to achieve a goal. This understanding leads to an organization that is based on processes. It places the emphasis on flow. With this perception, it becomes clear that a traditional top-down, siloed organization can no longer be an appropriate solution; it masks the inherent interconnectedness of work and prevents speed of flow. Understanding an organization as a system reveals the importance of interdependencies, including those with the customer. As with any system, feedback from the surrounding environment is an essential part of the picture. This creates awareness that the organization is part of a much bigger picture of value creation. The second fundamental element in Deming’s teaching is the importance of understanding and managing variation in the way that processes work. This creates a company focused on Quality and enables continuous improvement to provide goods and services that are predictably reliable.
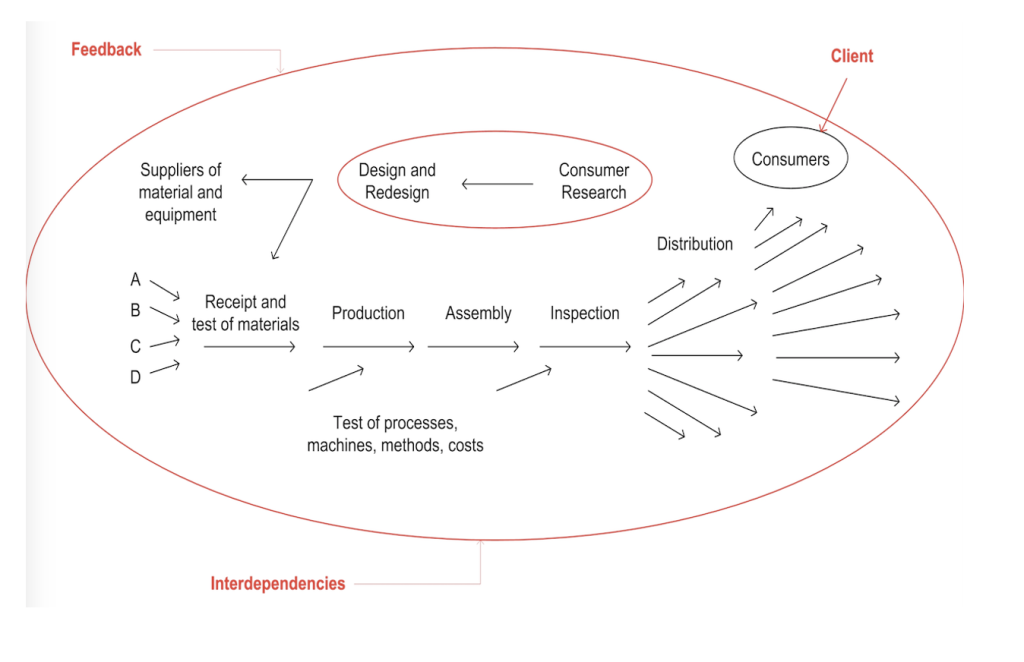
Another physicist, Dr. Eliyahu Goldratt, introduced a powerful concept that allows any organization to radically improve its performance. By identifying a strategic “constraint” in the system, we achieve a focusing mechanism that enables synchronization among all the components of the system. Prioritizing where to invest energy and cash becomes much simpler because any attempt to optimize parts of the system that do not contribute directly to the performance of the constraint is futile. Dr. Goldratt also developed systemic protocols for production, project management, marketing and sales and supply chain. It took nothing less that a team of physicists, mathematicians, engineers and philosophers to cohesively integrate the foundational principles of Deming’s work and TOC and elevate them to the level of whole system management and organization design. The resulting methodology is called the Decalogue and it has been transferred successfully to dozens of organizations in Europe and North America. (See ‘Quality Involvement, Flow: The Systemic Organization’)
Management or leadership?
When a company recognizes that it is inherently a system, it quickly sees that certain conventional approaches to management no longer make sense. What matters most is to operate clearly defined processes so that information, communication, production and cash generation can flow. Reporting is not vertical because there is no vertical. Middle management disappears because there is no middle with a bottom below it and a top above it. Everybody knows where their inputs come from and where the output they produce goes. It is clearly visible how everybody contributes towards the goal. Career paths are based on expanding responsibility rather than “climbing a ladder”. The role of leadership is not to give orders (the command and control model) but to enable people to carry out their jobs in the most effective and satisfying way. This is management.
Systemic management skills: managing variation
Systemic management means shifting away from trying to optimize “pieces” of the organization in a traditional, linear way towards whole system optimization. It would be impossible for leaders and managers to be expert in all aspects of systemic management and it is not necessary. As a foundation, leaders and managers must gain an understanding of complexity as the defining feature of our reality. This is because their work is to guide how the network of interdependencies occur so the organization can achieve its maximum potential. Being able to “see” the system entails mapping and flowcharting processes, making sure that tasks transform inputs into outputs. Every process is affected by variation. As Dr. Deming stated, the job of managers is to reduce variation. This makes mandatory an understanding of variation and how to measure and manage it using Statistical Process Control. This is the way to build predictability into the processes.
Systemic management skills: managing a constraint
For all the processes to deliver the goal of the organization, a synchronization mechanism is required. This can be achieved by strategically choosing a constraint, creating a buffer (Buffer Management) and managing all the activities of the organization so the constraint is working all the time. In a traditional approach, maximum efficiency is sought by exploiting capacity from every element of the system but in the systemic approach, we understand that this is a fallacy. This is because we cannot ignore the interdependencies among the different parts of the system and the variation that affects them. We must focus on the performance of the constraint and managing variation to ensure whole system optimization.
Systemic management skills: problem busting, decision making and innovation
When we understand that an organization is a system, it also requires us to adapt the way we think. Dr. Goldratt designed a set of Thinking Processes that greatly enhance people’s ability to think systemically. They develop the ability to “see dots and connect them” and to plan actions that are consistent with a well-identified goal. The Thinking Processes can be used to solve day-to-day conflicts as well as to design overarching strategies and develop breakthrough solutions. They strengthen people’s abilities to identify problems and make effective decisions. Using these Thinking Processes expands people’s cognitive horizon; by regularly challenging assumptions and mental models, the company learns to embed not just continuous improvement but continuous innovation into their day-to-day. (See ‘The Human Constraint’.)
Systemic management skills: project management
Ultimately, there are two kinds of activities that take place in an organization at any given time: repetitive processes and one-off projects. Sadly, the majority of projects fail to complete within budget and on time. This is due to the lack of a clear goal for the project, lack of planning and unrealistic expectations, given the resources available. As part of the Theory of Constraints, Dr. Goldratt developed the Critical Chain approach to Project Management. This sees the project as a system and therefore removes protection from individual tasks (the pieces) and protects the whole from inevitable variation with a buffer of time at the end of the project. Critical Chain works with the understanding that available capacity for the project is finite and it overcomes resource contention so that any completion date is realistic. Combined with the Thinking Processes to set an accurate goal and create robust planning, Critical Chain can ensure a radically higher number of successful projects. In a more recent innovation (see Intelligent Management’s book ‘From Silo to Network: A New Kind of Science for Management’), an organization can be envisioned and managed as a network of projects. This creates a level of synchronization that accelerates the flow within the organization and provides a new level of visibility of everything that is being managed within the system at any given time.
It’s up to you
The pace of change that we are experiencing in the world requires an unprecedented ability to:
- design and manage organizations in a way that they are inherently resilient and able to scale;
- continuously innovate for the market.
These requirements cannot be achieved by relying on outdated approaches to management that are blind to a conceptual and operational understanding of complexity. The work has been done to create solutions for a truly contemporary way of managing organizations. The knowledge, method and tools exist so companies can express their full potential and scale, unencumbered by a limited ability to interpret reality. Some learning is required, but as Dr. Deming said, “Learning is not compulsory, neither is survival.”
We can go well beyond survival and learn to flourish. It all starts with how we think and our willingness to challenge assumptions to find powerful solutions. We have created a new set of programs so organizations can learn to keep up with the pace of change by learning the Thinking Processes from the Theory of Constraints. Please visit our page Our New Programs for Systemic Thinking Processes.
To find out more about ten guided steps to a systemic leap in performance for your company, contact Angela Montgomery at: intelligentmanagement@sechel.ws
SCHEDULE AN INTRODUCTORY CALL WITH US
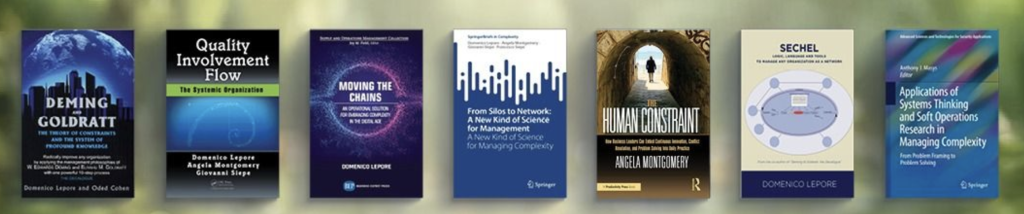
Intelligent Management works with decision makers with the authority and responsibility to make meaningful change to optimize your company for the digital age. We have helped dozens of organizations to adopt a systemic approach to manage complexity and radically improve performance and growth for over 25 years through our Decalogue management methodology. The Network of Projects organization design we developed is supported by our Ess3ntial software for multi-project finite scheduling based on the Critical Chain algorithm.
See our latest books: The Human Constraint from Routledge; From Silos to Networks: A New Kind of Science for Management from Springer; Moving the Chains: An Operational Solution for Embracing Complexity in the Digital Age by our Founder Dr. Domenico Lepore, and ‘Quality, Involvement, Flow: The Systemic Organization’ from CRC Press, New York by Dr. Domenico Lepore, Dr. Angela Montgomery and Dr. Giovanni Siepe.
Leave a Reply